Manufacturing has been returning to these shores for a number of years now, but the pace at which new factories are going up now is a wonderful surprise. The need for better quality control, lower shipping costs, faster time-to-market, and more reliable supply chains: these motivations are driving this boom. It’s about time. The Wall Street Journal recently reported this astonishing news: “Construction spending related to manufacturing reached $108 billion in 2022, Census Bureau data show, the highest annual total on record—more than was spent to build schools, healthcare centers or office buildings.”
This is a fundamental change that harbingers good things for America’s future. Nothing creates new value like manufacturing, and nothing else pays workers as well. Manufacturing was crucial to America’s Golden Age in the 50s and 60s and into the 70s when American industry was in its glory. It’s no accident that standards of living, during those decades, were good and getting better. As automation replaces more and more human beings in manufacturing processes, the newest jobs for people require higher learning and more advanced skills. A manufacturing worker isn’t an assembly line drone, but a highly skilled operator who is constantly finding ways to improve and innovate.
Many of the new factories are building electronics components and EV car batteries—as would be expected—but manufacturing is growing also in little niche markets too: eyeglasses, bicycles, body-building supplements. A sock manufacturer in California has constructed a new factory, moving operations back from outside our borders, to be able to respond very quickly to demand for commemorative clothing during events like NBA finals and Kentucky Derby. The pandemic woke everyone up to our dependency on foreign manufacturing and the way it has throttled our response to rising demand for products following the lockdown.
The Wall Street Journal quoted UBS industrials analyst Chris Snyder: “Covid kind of pulled the covers off and showed everybody how much risk they were exposed to.”
At 13 million jobs, total manufacturing employment still represents only 10 percent of the economy even with the addition of 800,000 new workers in the past two years. A good part of this boom can be traced to government stimulus being pumped into semiconductors and electric vehicles. But it’s happening well outside those industries.
A recent McKinsey study explains that what’s happening now is only the beginning of a tidal shift in the global economy, sweeping more and more manufacturing back to within our borders. Manufacturing, the consulting firm predicts, would boost GDP in the U.S. by 15 percent over the next decade: “Our analysis suggests that reviving manufacturing could add up to 1.5 million jobs, particularly among middle-skill workers, which would help recalibrate the US labor market and bolster the middle class.” Not only will this boost total economic output, the quality of these jobs will help offset rising income and wealth inequality. Manufacturing growth, as the study puts it, means “inclusive growth.”
As much of the manufacturing process returns to America, shorter distances between factory and suppliers and customers make the entire process easier to control and scale up or down when demand shifts. “Companies develop shorter, more resilient, and more adaptable supply chains that better serve the needs of different markets.” Proximity offers deeper and more personal partnerships between manufacturers and their regional suppliers, as well as with customers and employees. The possibility of face-to-face relationships opens up the opportunity for a more robust and responsive system for creating customer delight.
Skeptics will point out that this migration of manufacturing back to American shores does indeed bring jobs back home, yet the need for new facilities offers a chance to invest in the latest digital systems and automate much of what human workers once did. A facility that employed dozens in Mexico or China may employ only a dozen in South Carolina and a decade from now may employ only three or four highly skilled operators. This is the seeming paradox of a manufacturing renaissance: while America regains its manufacturing muscle, manufacturing itself is shedding the need for human muscle.
Yet this isn’t as paradoxical as it may seem. First, manufacturing isn’t manual labor now: the new jobs require people who understand computer tech and robotics as well as sophisticated logistics. What’s not immediately apparent is how a manufacturing facility that springs up in Kansas City creates jobs all around it through the growth it generates among suppliers, transportation, and the income it brings to the community’s restaurants, supermarkets, and so on. And with the money that went into wages, a manufacturer can open new facilities and enter new markets, thus generating jobs.
The new manufacturing will encourage a close partnership with all these other stakeholders. In fact, the McKinsey study sounds like an invitation to the multiple stakeholder model with a focus on innovation and creativity as the source of value: “To succeed, therefore, companies will need a solid financial and operational plan that is aligned at all levels of the organization and spells out detailed actions and clear responsibilities for all stakeholders. Large-scale changes to manufacturing processes and footprints may take 10 or 20 years, and breaking away from the status quo will require creativity, commitment, and significant innovation.”
It points out that education will become a core competency for any manufacturer who wants to keep up in a more competitive market. Digital and automated technologies are constantly being upgraded. Training for operators has to be an on-going, in-house curriculum, in a sense. Employers are advised to become training centers themselves and “skill builders.”
As automation eliminates certain jobs, it generates many more. So much of what Amazon
AMZN
If we don’t pay people enough, we end up relying on entitlements to provide them with what they need for a good life. We kick the can of that responsibility to the government, and it will tax and spend in order to make a certain quality of life possible. We give people a fair wage directly as their employer or we delegate that role to government through taxation. In that case there is tremendous waste, all the administrative costs associated with taxation and the complex process the so-called government entitlement benefits.
Larry Summers has talked about rising wages as a driver of inflation. Yet rising wages don’t come close to the inflationary effect of flooding the economy with economic stimulus—compared to the gentle stimulus generated by wages that stay ahead of the cost of living. Conversely, stagnant wages create horrible problems down the road: increasing consumer debt, the despair of never being able to save for the future or help provide for college, and the social disruptions that follow.
The core of stakeholder capitalism is to build trust and loyalty and motivation by treating each worker as a potential profit center: a source of creative ideas for improvement that open new markets and make existing ones more profitable. When treated with respect and care, employees aren’t a cost, but just the opposite: they are the source of your profit. Only motivated, highly engaged employees have the will and desire to help increase a business’s productivity and drive for innovations in products and processes.
This resurgence of manufacturing is a perfect opportunity for CEOs to adopt the stakeholder capitalist model that, essentially is the only way to dramatically increase profitability and long-term value creation. This remarkable opportunity is there, already working in dozens of companies, waiting to be embraced.
Read the full article here
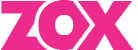