© Reuters. FILE PHOTO: Containers are seen on a shipping dock, as the global outbreak of the coronavirus disease (COVID-19) continues, in the Port of Los Angeles, California, U.S., April 16, 2020. REUTERS/Lucy Nicholson/
By Lisa Baertlein
CHICAGO (Reuters) -Some U.S. importers who shifted cargo away from West Coast ports to rival gateways over fears that labor contract talks could disrupt shipments have begun bringing some of that volume back, even as those negotiations stretch into their 13th month, company supply chain executives said.
But anxiety over labor negotiations only explains part of the market share losses at West Coast container ports, including the nation’s busiest at Los Angeles/Long Beach, nine importers said at the Reuters Events Supply Chain conference this week in Chicago.
That is because retailers and suppliers, ranging from Sharpie pen and Rubbermaid storage products maker Inc to nursery furniture seller Million Dollar Baby, have been reworking distribution strategies and sending goods to the East Coast and Gulf of Mexico to position goods closer to where consumers live.
“There is probably a 10% gap that they will never get back,” said Regina Diaz, director of operations at Los Angeles-based Million Dollar Baby, which was already shipping goods to new distribution centers near the New Jersey and Savannah, Georgia, ports when the West Coast labor talks began last May. Customers on the U.S. East Coast account for 70% Million Dollar Baby’s demand, company executives said.
Large and small retailers have been diverting cargo away from West Coast ports since before the contract covering 22,000 dockworkers at ports stretching from California to Washington State expired on July 1, to avoid any repeat of labor disputes that in the past have stranded goods on docks or ships.
During the first three months of 2023, West Coast ports handled 40% of U.S. container import volume. They handled 45% of cargo during the same period in 2019, before the pandemic struck, according to data from Descartes (NASDAQ:) Datamyne.
Extrapolating that first-quarter data over 12 months would show that more than 1 million twenty-foot equivalent units (TEU) moved away from the West Coast ports annually, starting in 2021, said Chris Jones, an executive vice president at Descartes Systems Group .
Colgate-Palmolive (NYSE:) Co routed 25% of containers away from West Coast ports and has already begun reversing some of that, said Francisco Rodriguez, Colgate toothpaste maker’s director of global logistics.
The labor negotiation process, while lengthy, “is working like it is supposed to,” said Rodriguez, who added that his team monitors port activity daily and makes decisions based on that – rather than headlines about union negotiation-related conflict.
“The rebalancing will inevitably happen,” said Michael Schetman vice president of North American sales for APL Logistics. That is because ocean shipping from China to Los Angeles remains the fastest and cheapest option, he said.
Kevin Austin, group vice president of demand and supply management at Toyota Motor (NYSE:) North America, declined to comment on the automaker’s cargo volume trends at Los Angeles’ port complex, and like other importers said the facility remains “critical” to their businesses.
The Port of Los Angeles on Thursday said April volume was down from last year’s record levels but up for the second consecutive month.
Meanwhile, the Southern California ports face new pressure from outside the U.S., importers said.
About six months ago, Million Dollar Baby started sending some upholstered furniture with price tags of under $800 per piece from China into the port at Ensenada, Mexico.
Importing to Mexico opens a legal loophole that enables Million Dollar Baby to sell those products to U.S. customers without a 25% tariff. Warehouse and labor costs are also lower in Mexico than in the U.S., adding to savings, Diaz said.
Read the full article here
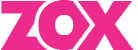